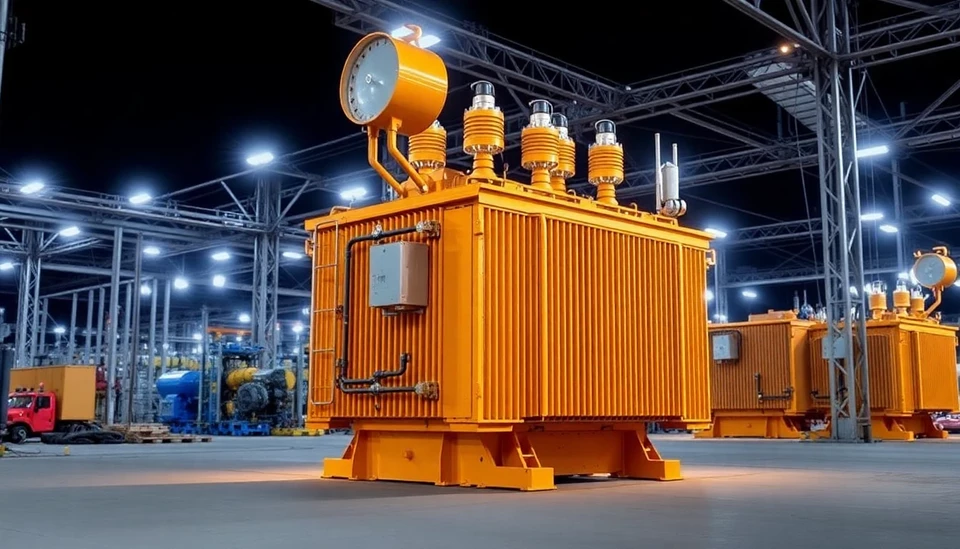
The year 2025 is poised to be a pivotal moment for the transformers industry, as manufacturers grapple with significant bottlenecks in production and supply chains. A confluence of factors including rising global demand, shifts in production capabilities, and geopolitical tensions are influencing how transformers are designed, produced, and delivered. Engineers and manufacturers are already feeling the impact of these dynamics, which promise to alter the landscape of the industry for years to come.
As renewable energy sources continue to gain prominence, the demand for transformers, which are essential for voltage regulation and the transfer of electricity, is skyrocketing. The growth in electric vehicle (EV) infrastructure further heightens the need for robust transformer systems capable of handling increased load demands. But this surging demand is met with a looming crisis: supply chain interruptions and raw material shortages linked to global production shifts are raising alarms among key stakeholders.
Many organizations within the transformers sector have reported significant delays in the procurement of essential components. Compounding these delays are logistical challenges exacerbated by ongoing geopolitical tensions, particularly those arising from tariffs and trade restrictions. As international markets fluctuate, manufacturers find themselves navigating a complex landscape of obstacles that threaten to impede progress.
The technological evolution of transformers is witnessing unprecedented shifts as companies strive to innovate in efficiency and sustainability. Advanced materials and smarter designs are being prioritized, yet manufacturers face the challenge of sourcing these innovative components amidst persistent supply chain bottlenecks. Furthermore, the urgency to improve energy efficiency and reduce carbon footprints adds another layer of complexity to the manufacturing process.
Industry leaders are responding by reassessing their strategies to mitigate the impact of these bottlenecks. Measures include diversifying supply sources, investing in automation technology, and adopting advanced manufacturing techniques aimed at optimizing production efficiency. Collaboration across the supply chain has emerged as a critical approach to identify and resolve inefficiencies, with several companies forming alliances to bolster their resilience in the face of these challenges.
The implications of these bottlenecks extend beyond manufacturers; energy producers, utility providers, and consumers alike stand to be affected. Delays in transformer production could translate to interruptions in the installation of critical infrastructure projects, potentially slowing the transition to greener energy solutions. The ripple effect highlights the interconnected nature of the energy sector, where delays in one segment can have far-reaching consequences.
As we edge closer to 2025, the transformers industry must balance the pressing need for innovation with the realities of a constrained supply chain. Stakeholders throughout the energy ecosystem are urged to remain vigilant and proactive as they navigate this complex landscape, with hopes that concerted efforts will lead to enhanced efficiencies and sustainability in the long run.
#TransformersIndustry #SupplyChainChallenges #RenewableEnergy #GeopoliticalTensions #ElectricVehicles #ManufacturingInnovation #EnergyEfficiency
Author: Sophie Bennett